Byrne Dairy
Onondaga County
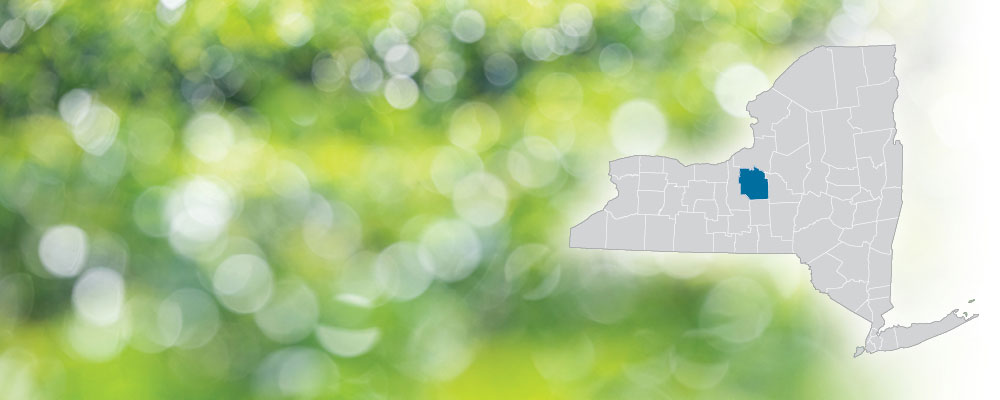
Processing Savings with On-site Energy Manager
Overview
Founded in 1933, Byrne Dairy (Byrne) is a regional dairy company with several locations in or near Syracuse, NY. After successfully integrating energy management principals at their Ultra High Temperature manufacturing plant, Byrne enrolled three other facilities in the New York State Energy and Research Development Authority’s (NYSERDA) On-site Energy Manager program.
Each location is unique in the type of product that is produced; however, the facilities generally consist of processing, filling, packaging, and sterilization. The process support systems include ammonia refrigeration, hot water and steam boilers, ovens, compressed air, and cooling towers.
Project Spotlight
Company Name:
Byrne Dairy
Industry:
Dairy Processor
Location:
Syracuse, NY
Planning Action
CHA Consulting, Inc, a full-service engineering consulting firm, served as the part-time On-site Energy Manager over a 16-month period to improve and maintain Byrne’s operational and energy efficiency.
CHA provided a team of two engineers to perform the duties of the energy manager. General responsibilities included providing technical assistance, training, identifying opportunities, promoting continuous improvement, implementation of energy management strategies and projects, and verifying results. The energy manager needed to become familiar with multiple locations and plant personnel, which required a detailed management plan including scheduling on-site time for each location and facilitating collaboration between numerous people. The site energy reduction goal was to achieve a 5% reduction in energy consumed.
Reducing Energy Use
A total of 30 potential energy projects were identified across the three active facilities. The projects were all completed at Byrne’s Ice Cream Center facility; six of the 11 total projects installed during the engagement had a total capital investment of $23,726. The cost savings from the installed projects totaled $13,841, resulting in a simple payback of 1.5 years after accounting for $2,921 of incentives received. In addition to energy savings, several projects had ancillary maintenance savings benefits.
Target | Installed (Acquired) Progress | Identified (Pipeline) Progess | % Installed Progress Against Target | % Identified Progress Against Target |
|
Annual Electric Energy Savings, kWh | 534,790 | 153,741 | 1,057,705 | 29% | 198% |
Annual Gas Energy Savings, MMBtu | 1,820 | 0 | 4,406 | 0 | 242% |
Sharing Results
Although each location at Byrne Dairy produces different products, each site had similarities and benefited from collaborating and sharing procedures and successes. Each facility had similar process support equipment and the ability to apply similar energy-saving concepts. As an example, recent lighting retrofits were replicated across all the facilities. With a common corporate and engineering group across all facilities, the trainings and energy procedures, such as compressed air best practices, introduced through the Energy Management program can be maintained across the company.
The NYSERDA On-Site Energy Manager Program
Through OsEM, NYSERDA cost-shares the cost to hire an OsEM. OsEMs work with companies to develop and implement successful energy and productivity projects. Projects may include operation and maintenance improvements, behavioral changes, energy efficiency upgrades, process improvements, throughput and scrap reduction improvements, and cost management.
Discover how to bring energy costs under control and improve profitability.
Visit nyserda.ny.gov/OSEM