Byrne Dairy
Onondaga County
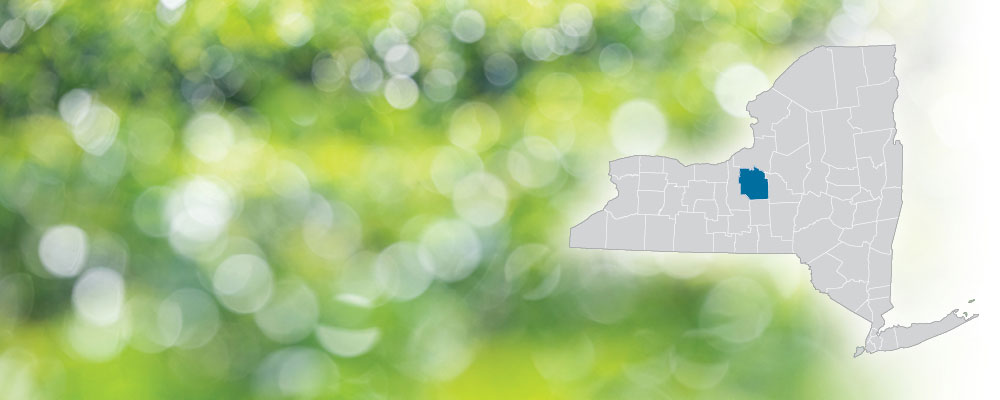
Byrne Dairy is Processing Energy Savings with On-site Energy Manager
Overview
Located in East Syracuse, NY, Byrne Dairy opened the Ultra Dairy Facility as a 40,000 sq. ft Ultra High Temperature (UHT) pasteurization manufacturing plant in 2004. By 2016, the plant had grown to 140,000 sq. ft with the capacity for future expansion. The UHT milk process involves several steps such as receiving, storing, separating, blending, pasteurizing, homogenizing, filling, packaging, and palletizing. The process support systems include ammonia refrigeration, steam, compressed air, and cooling towers.
With a commitment to providing the community with the highest quality products while minimizing the facility’s environmental footprint and conserving natural resources, Byrne participated in the New York State Energy and Research Development Authority’s (NYSERDA) On-Site Energy Management program. Through the program, Byrne contracted CHA Consulting, Inc.—a highly diversified, full-service engineering consulting firm—for a full-time On-site Energy Manager at Byrne over a 13-month period to improve and maintain the facility’s operational and energy efficiency.
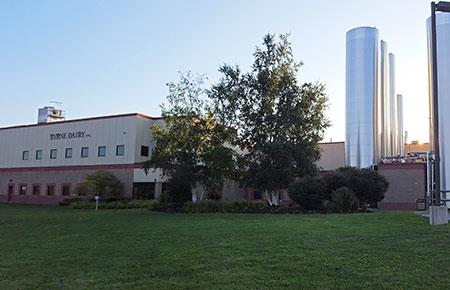
Preparing the Plan
CHA provided a team of two engineers to perform the duties of the energy manager. General responsibilities of the team included providing technical assistance, training, identifying opportunities, promoting continuous improvement, implementation of energy management strategies and projects, and verifying results. The site energy goal was to achieve a 5.5% reduction in energy consumed. During the energy management engagement, it was noted that Overall Equipment Effectiveness (OEE) on several product lines were negatively impacted by machine breakdowns, alignment problems, waiting on product, and lower speed settings. The inefficient use of equipment wastes energy while processes are idling but not producing useful products.
Engage Everyone At All Levels of the Company
“Engaging and leveraging the existing knowledge is essential towards the short- and long-term success of energy management. Instead of conceptualizing projects exclusively with the engineering group and management, the other groups at the company should be considered for input.”
— Byrne Dairy
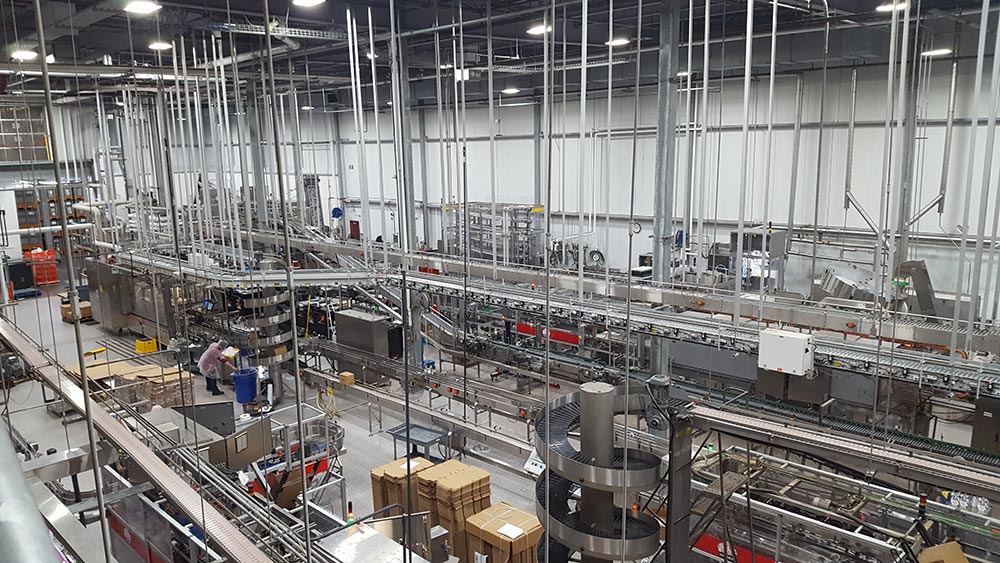
Producing Results
A total of 41 energy projects were identified, and 11 projects were installed during the engagement with a total capital investment of $324,096.32. The total cost savings from the installed projects total $131,575.42, resulting in a simple payback of 2.5 years. In addition, several projects had ancillary benefits such as product, O&M, water, and boiler chemical savings.
Total | Installed (Acquired) Progress | Identified (Pipeline) Progess | % Installed Progress Against Target | % Identified Progress Against Target |
|
Annual Electric Energy Savings, kWh | 1,052,053 | 684,054 | 734,177 | 65% | 70% |
Annual Gas Energy Savings, MMBtu | 11,757 | 19,817 | 15,314 | 169% | 130% |
Moving Forward
Byrne Dairy has embraced lean manufacturing and continuous improvement practices over the last several years as part of a corporate-wide initiative. Near the end of the engagement, Byrne Dairy engaged the CHA Energy Manager to help launch a Total Productive Maintenance (TPM) program along with a Lean manufacturing initiative with the intent of changing the culture at the plant for continuous improvement and waste elimination. The TPM program will focus on improving preventative maintenance and procedural programs to eliminate downtime and waste.
Discover how to bring energy costs under control and maximize profitability.
Visit nyserda.ny.gov/OSEM