St. Marks Passive House
Kings County
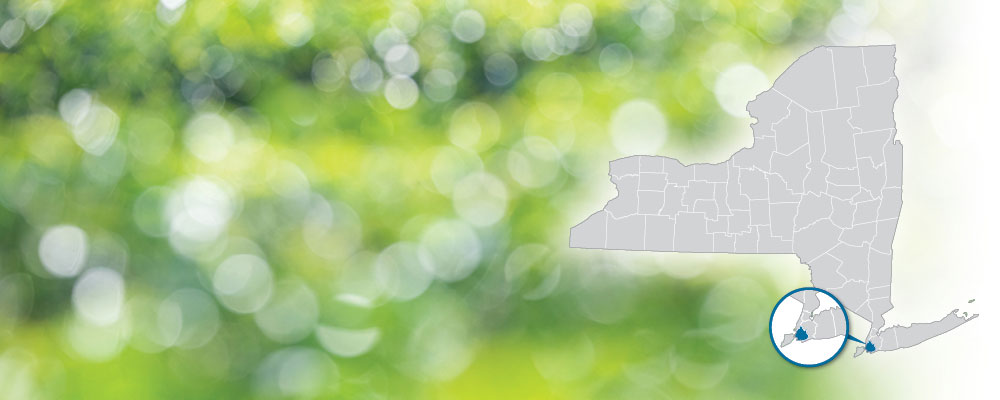
Multifamily, All-Electric, Carbon Neutral, Net Zero
Background
St. Marks is a 10-unit urban infill project in Brooklyn, NY. The project was taken on by a European developer, Masmark LLC, with the vision of creating a well-designed and highly energy-efficient residential building. Designed to be architecturally synonymous with the historical context of the neighborhood, the project will be an all-electric building, expected to achieve Passive House Institute (PHI) certification. The project features a high-performing and well-insulated envelope, thermal bridge reduction, triple-glazed PHI certified windows, and strategically shaded windows on the southern face. The design team also utilized strategies to increase the building’s resiliency and occupant health and comfort, such as on-site solar power, green walls, and airtight construction techniques.
Key Project Features
The project follows PHI principles to achieve a highly efficient design, such as incorporating a compact and simple form. Other improved performance strategies include on-site stormwater management; transit-oriented development; and all-electric equipment and appliances. Energy efficiency strategies include:
- HVAC: Variable refrigerant flow (VRF)-air source heat pump (ASHP), energy recovery ventilation (ERV)
- Water Heating: COLMAC CxV-5 ASHP
- Envelope: Panelized
- Passive: Passive House Institute (PHI) certification
- Lighting: Light emitting diode (LED) with controls
- Appliances: Electric dryers, induction stoves
- Renewables: Onsite photovoltaics (PV)
- Resilience Strategies: High-performance envelope
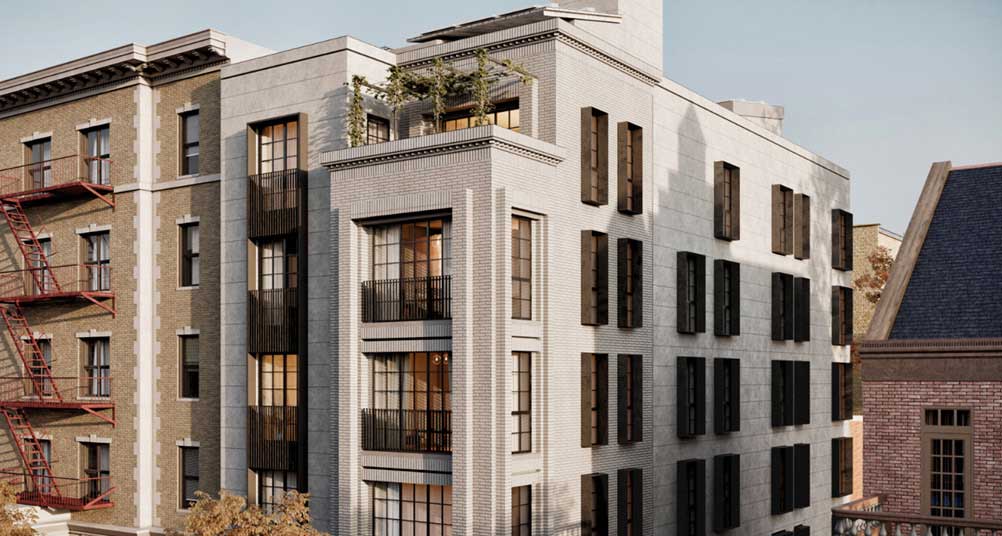

Rendering of southeast corner of building, provided by Cycle Architecture + Planning
Project Details
- Location: Brooklyn, New York
- Project Area: 17,303 SF
- Number of Buildings: 1
- Number of Stories Per Building: 5
- Number of Units: 10
- Project Cost: $5,661,080
- Cost per Gross Square Foot: $355.42
- Market Sector: Market Rate
- Construction Type: New Construction
- Construction Start Date: April 2021
- Completion Date: December 2022
- REDC Region: New York City
- Developer: Masmark LLC
- Architect & Design Team Lead: Cycle Architecture + Planning
- Technologies Used: Manufactured & panelized clip-on façade, VRF, ERV, PV
- Predicted Site Energy Use Intensity (EUI): 7.7 kBtu/SF/yr
- Net Site Energy Use Intensity (EUI)*: 4.2 kBtu/SF/yr
- Predicted Renewable Production Intensity (RPI): 3.5 kBtu/SF/yr
- Energy Code Baseline: 2016 NYS Energy Conservation Construction Code (ECCC)
- Performance Path: PHI Certification: PHI
*EUIs calculated using "Building Area." The "Treated Floor Area" used in the energy model is 32% smaller, which would lead to EUIs 48% larger than shown
Planning and Design Approach
Project Goals
St. Marks Passive House began as a real estate venture by Masmark LLC, a European developer based in Italy, who had the vision of creating a well-designed and extremely energy-efficient building. The design team was challenged with creating a project that met the PHI certification standards. The criteria a building must meet to achieve PHI certification include: a space heating energy demand that does not exceed 15 kWh/m2 treated floor area (TFA)/year, a total energy use for all domestic applications that is less than 60 kWh/m2 TFA/year, and a maximum of 0.6 ACH50.
All PHI certification requirements can be met through the design application of the five Passive House principles : quality insulation, reduced thermal bridging, superior windows, adequate ventilation, and airtight construction.
Project Team
The success of the project is due largely to the development of close working relationships between the design team from Masmark LLC and the design consultants.
The project team brought on a construction manager, PHB Catalyst Group, early in the process to provide feedback at schematic and design development phases. PHB Catalyst Group continued to provide pricing feedback at each step, allowing the design to progress within the budgetary constraints. Through this collaborative review process, the team discovered that the biggest opportunities to save both time and money would be in the design and incorporation of the building structure, foundation, site connections, and plumbing systems.
A marketing team, Compass, was also engaged early on. They, along with Masmark LLC and Cycle Architecture + Planning, worked to understand the market and where energy-efficient design could fit into the overall marketing plan. This plan was influential to the early design phases.
Both a Passive House certified tradesperson and a representative for the owner were brought on to supervise the construction process. The team also worked with two architects from Cycle Architecture + Planning that are a Certified Passive House Designers and a mechanical, electrical, and plumbing (MEP) engineer from EP Engineering who is familiar with Passive House principles, ensuring that the whole team would be able to both identify and apply various strategies successfully throughout the entirety of the design process. Structural Engineering Technologies served as the structural engineers for the project. The contractors also participated in training and testing sessions during the construction phase to make sure that all aspects of the project were constructed and installed to Passive House standards.
Building Design
St. Marks is a 10-unit multifamily residential building in Brooklyn, NY. The architectural design and details of the building’s exterior are conscious of the historic context of the Crown Heights neighborhood, whose streets are lined with brownstones. Along with the Passive House principles, the design team considered energy-efficient strategies and building performance best practices as crucial starting points for the design process.
The project features a well-insulated building enclosure, including thermal bridge reduction, triple-glazed and thermally broken Passive House Institute certified windows, deeply shaded windows on the south side, energy recovery ventilation, and a highly efficient VRF system for heating and cooling. The project team made intentional design decisions, particularly through material selection, that not only added to the energy efficiency of the building and its construction, but also provided environmental benefits. Mineral wool and dense pack cellulose were used in place of polyiso and other plastics, Forest Stewardship Council (FSC) certified wood was used, finishes were made from recycled content and no-spray foam was used in the entirety of the project. Other sustainable design strategies include an efficient waste management system, which follows NYC Zero Waste Design Guidelines; on-site stormwater management through a simply engineered retention system; and green walls consisting of native plants on the south and east facades. The project has the potential to become a new model for high-performing urban infill housing.
Energy Modeling
Seeking PHI certification, the building was modeled using Passive House Planning Package (PHPP) Version 9.7 IP software. The model includes 11,690 SF of treated floor area, and the project team modeled two thermal bridges with Ψ-values of 0.1 and 0.08. The HVAC system is modeled as an LG 16 seasonal energy efficiency ratio (SEER) ASHP with a maximum cooling capacity of 366 kBtu/hr and supply of 9,153 cubic feet per minute (cfm) at nominal power. The domestic hot water (DHW) system, which was originally modeled as a gas condensing boiler, is modeled as a COLMAC heat pump with 180 gallons of storage. This change in DHW systems resulted in a 63% reduction in energy demand for DHW. Other loads include electric stoves, LED lighting, electric exhaust clothes drying, and an elevator. The model expects PV generation of 17,556 kWh/year. The Primary Energy Renewable (PER) demand of 14.1 kBtu/SFyr currently defines the building as a Passive House Plus Building. The most recent model improves on the first iteration of the design and was able to be pre-certified for the Passive House standard.
Energy Efficient, All-Electric Design
High-Efficiency Lighting Fixtures and Appliances
There is LED lighting throughout the project, both on the interior and exterior. In their commitment to creating a carbon neutral building, the project team included all-electric and efficient equipment and appliances in each unit. The laundry machines include a heat pump clothes dryer and each kitchen has an induction cooktop.
Building Envelope
The project was designed with an energy efficient, high-performing building envelope.
The Klearwall Passiv Alu-clad windows have a U-factor of 0.15 and a solar heat gain coefficient (SHGC) of 0.57.
The above grade walls have a U-value of 0.02, a window-to-wall ratio of 29%, an average façade U-factor of 0.03, and an airtightness level of 0.06 ACH50.
The roof has a U-factor of 0.015, and the below grade walls have U-factor of 0.026.
The design includes passive shading on the south face, and windows on all four faces for maximum natural daylighting. The typical exterior wall construction achieves an R-value of 49, which translates to a U-value of 0.02. From exterior to interior, the wall consists of:
- ½ inch to ¾ inch cement-board rainscreen panels
- an air gap
- R-16 4 inches rigid Rockwool comfort board
- Solitex Mento weather resistant barrier, which is an air tight, vapor-permeable house wrap
- 5/8" open vapor sheathing
- 6 inch metal stud with Rockwool insulation in the cavities that has a minimum R-value of 25
- Intello Plus or Sim Intelligent air barrier (to be determined)
- a furring channel with a nominal 2 inch service cavity, with the voids filled with R-6 1 ½ inch Rockwool comfort board
- 5/8 inch gypsum wall board
All Rockwool insulation within the envelope is a type of mineral wool insulation, eliminating the use of foam in the project.
This advanced envelope system ensures low thermal transmittance and reduced interior temperature fluctuations, which both improves occupant comfort and significantly reduces energy loads.
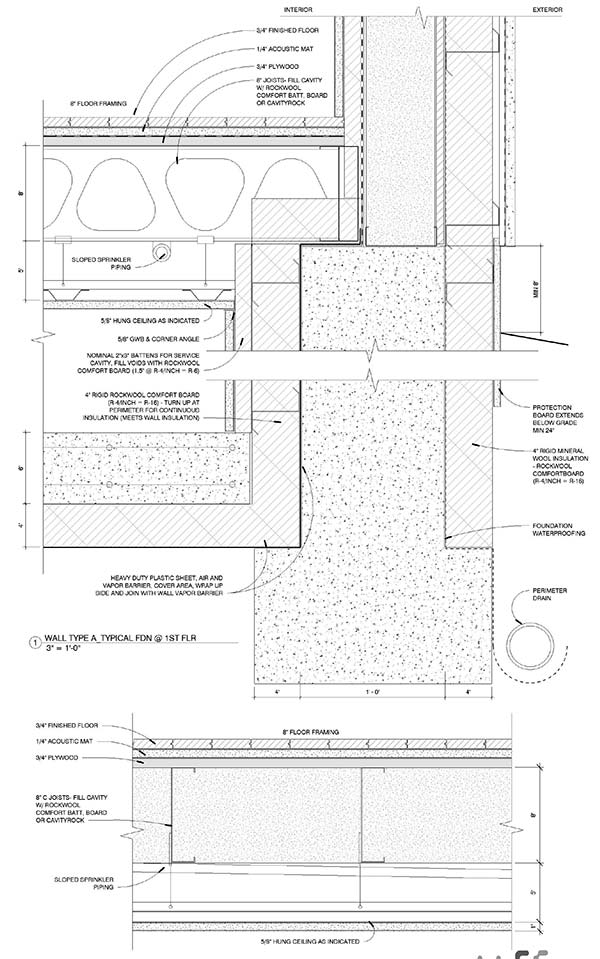
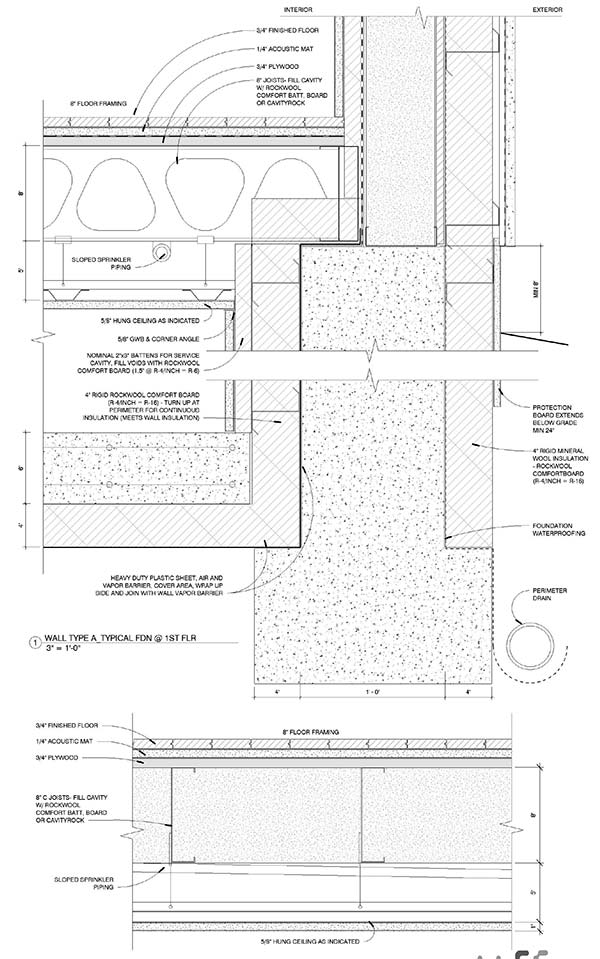
Download the full technical drawing [jpg]
Technical drawing of the building structure and envelope, provided by Cycle Architecture + Planning
All-Electric Systems
Heating is provided through ASHPs and the DHW is provided by a COLMAC CxV-5 electric ASHP water heater. The design originally included a semi-instantaneous gas condensing water heater, but to support the goal of achieving a project with no on-site fossil-fuel use, it was changed to an electric water heater. The ventilation is run on an ERV system.
Renewable Energy
The project includes a rooftop mounted solar array. Based on the energy model, the array is expected to generate 59,904 kBtu/year for a RPI of 3.8 kBtu/SF-year.
Energy Consumption Feedback and Smart Building Technologies
Energy monitoring systems are used for all apartments and common areas. Energy use is monitored by Fronius, which monitors all energy and water system performance, and provides a graphical display for owners to monitor their usage. Their online monitoring tool, Fronius Solar.web, provides real-time PV system data and usage analysis functions. The lights are controlled by occupancy sensors in all apartments, and both occupancy sensors and time-of-day sensors in all common areas. Lighting in stairwells and corridors will remain on all hours of the day but will dim and brighten based on occupancy. Time-of-day sensors are also used for all exterior lighting and corridors. The HVAC system includes controls for individual rooms and apartments, and both sensors and controls for the common areas through a humidistat. The hot water is electrically metered and monitored for the whole building, and the refrigerant is monitored by unit.
Commissioning
The Passive House Certification requires blower-door testing and the project team intends to encourage post-occupancy commissioning.
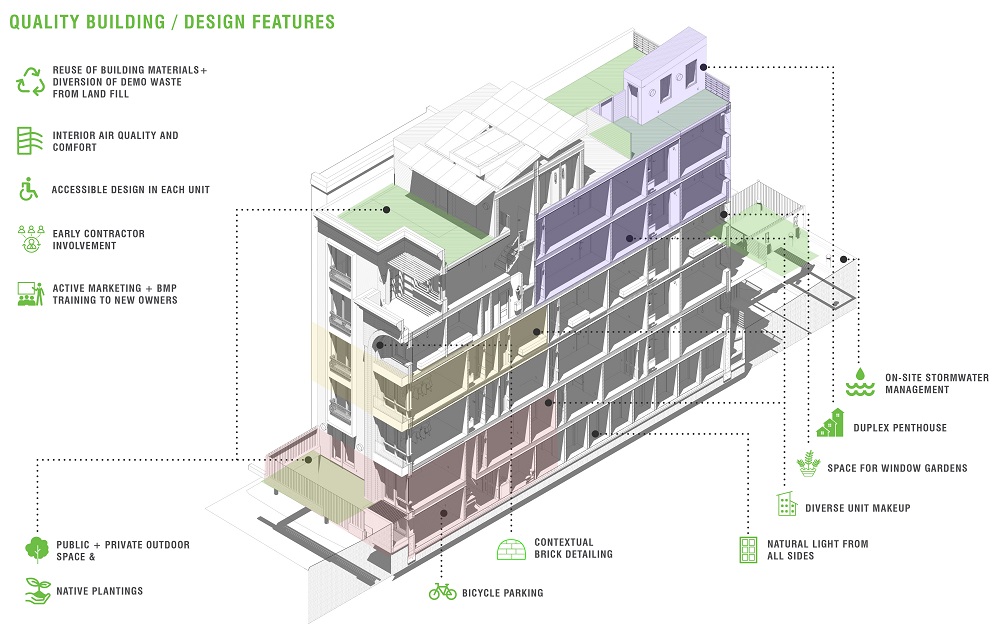
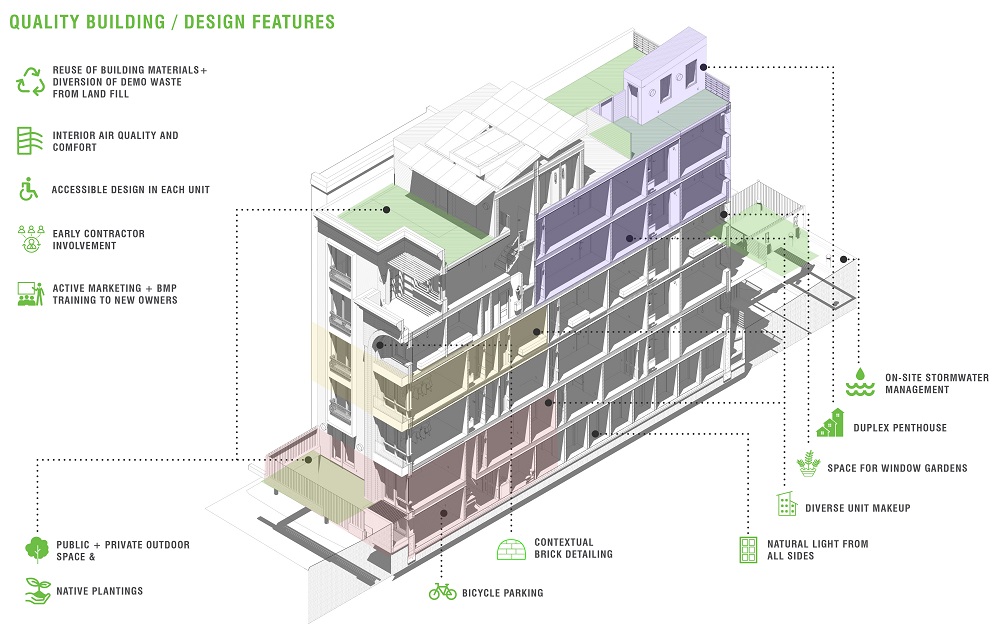
Rendering of south face of the building, provided by Cycle Architecture + Planning
View more about the rendering View more about the rendering
Quality Building/ Design Features
- Reuse of building materials and diversion of demo waste from land fill
- Interior air quality and comfort
- Accessible design in each unit
- Early contractor involvement
- Active marketing and BMP training to new owners
- Public and private outdoor space and native plantings
- Bicycle parking
- Contextual brick detailing
- Natural light from all sides
- Diverse unit makeup
- Space for window gardens
- Duplex penthouse
- On-site stormwater management
Building Operations
Leasing Structure
St. Marks will be occupied through a condominium structure and sold as market-rate units. Tenants will be directly metered for electricity, heating, cooling, and water. All energy and water systems will be monitored and graphically displayed for the owners.
Cost Reduction
The project is expected to be a market-rate condominium, comparable to similar buildings for both construction costs and relative sale prices. While the relative total per-resident energy cost has not yet been compared to other buildings, the building is designed to more efficient standards than the building code. Additionally, the energy is purchased in part from the on-site PV system, therefore, it is very likely that energy costs to residents will be lower than in other buildings of the same type.
Occupant Engagement
The best practices manual for all systems that are installed in the building will be outlined for the owners. The development team will also encourage healthy and green lifestyle practices among tenants by incorporating zero waste design principles, including easy ways for residents to collect and dispose of compost, waste, and recyclables. Each unit will be equipped with countertop organic bins for compost and pull-out cabinets with bins for waste and recycling. The collected organic material will be turned into compost and used in the site’s front and rear yards.
Additional Benefits
Site Context
The project is located in a walkable and urban neighborhood in Brooklyn, NY, earning a Walk Score of 98. There are also several parks and recreational facilities within a short walking distance. The area offers stops for local and express bus services, the regional rail service, the city subway, and several bikeshare docks, all within a half-mile radius of the site. St. Marks will add to and improve the density of the neighborhood.
Occupant Health, Comfort, and Productivity
As a candidate for Passive House Certification, St. Marks incorporates technology and strategies that improve the health, comfort, and safety of occupants, including HVAC controls and sensors in each room, well-ventilated spaces, radon resistant slab, plenty of natural daylight, accessible unit layouts, and mold-resistant construction. Each unit is designed to be handicap accessible, provide space for window gardens, and ensure good interior air quality. The building also provides bike parking in the basement to encourage carbon-free transportation.
Resiliency
The project, by following the Passive House criteria, inherently incorporates strategies for improved resilience, such as ensuring airtight construction and a high-performing building envelope. These design strategies increase the building’s passive survivability by limiting thermal transfer and keeping indoor temperatures at safe levels during grid outages. Onsite stormwater management, including a simple engineered retention system, will help to reduce excessive stormwater runoff which can lead to flooding and pollution.
Lessons Learned
- Beginning the project with a motivated developer who challenged the team to meet Passive House Institute (PHI) certification standards provided a strong framework for success.
- An integrated team working closely throughout the process was critical to the success of this project:
- A Passive House certified tradesperson and a representative for the owner supervised the construction process.
- Both the Architect, from Cycle Architecture + Planning, and the mechanical, electrical and plumbing (MEP) engineer, from EP Engineering, were already familiar with Passive House principles, enabling them to guide the team to identify and implement key Passive House strategies.
- The construction manager, PHB Catalyst Group, identified pathways to save time and money, keeping the project within the budgetary constraints. The building structure, foundation, site connections, and plumbing systems proved to be the largest source of savings.
- The marketing team, Compass, worked with Masmark LLC and Cycle Architecture + Planning to help the team to understand the market and where an energy-efficient design could fit into the overall marketing plan.
- Iterative design through energy modeling resulted in significant designed energy savings. For example, the domestic hot water (DHW) system was originally modeled as a gas condensing boiler and later replaced with a heat pump, resulting in a 73% reduction in energy demand for DHW.
- During construction, contractors participated in training and testing sessions to ensure the designed measures were installed to Passive House standards and the project was required to have a Certified Passive House Tradesperson (CPHT) on site during construction.
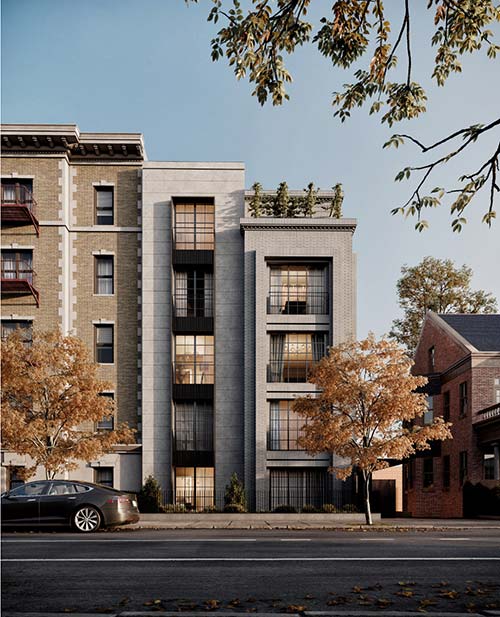
Ready to get started on new construction?
Contact NYSERDA at [email protected].