425 Grand Concourse
Bronx County
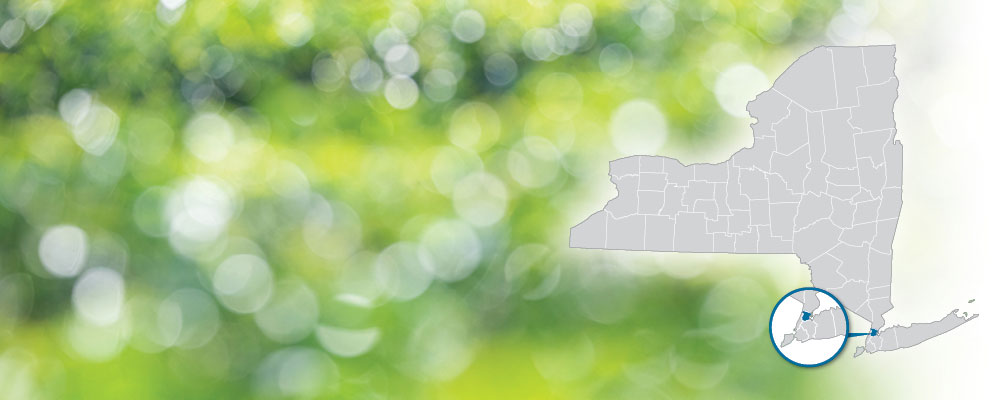
Mixed-Use, High-Rise, Affordable Passive Housing
Background
Trinity Financial’s 425 Grand Concourse is a 277-unit, mixed-use, and mixed-income affordable housing project in the Bronx. Through massing and site design, the project blends with the existing urban fabric while incorporating community-geared spaces for education, health, culture, and retail. The project team utilized an integrated design approach, bringing consultants, engineers, and contractors on early in the design process.
Designed to the Passive House Institute US Plus (PHIUS+) 2015 certification standard, 425 Grand Concourse is the largest PHIUS project to date among certified and pre-certified projects and is expected to have substantially reduced energy use and carbon emissions compared to a code-minimum new construction project. The project features a high-performance building envelope, daylit corridors, large-scale sunshades, and passive survivability strategies, such as backup power and water availability during extended periods without power. The development team hopes that this design can act as both a model and inspiration for other high-density, high-rise Passive House affordable housing projects.
Key Project Features
The 425 Grand Concourse project will incorporate highly efficient equipment throughout the design:
- HVAC: Variable refrigerant flow (VRF) air source heat pump (ASHP), energy recovery ventilation (ERV)
- Water Heating: Condensing boiler
- Envelope: Continuous mineral wool, concrete masonry unit (CMU) backup wall
- Passive Design: Passive House Institute US Plus (PHIUS+) 2015 certification
- Lighting: Light emitting diode (LED), daylighting
- Appliances: Electric heat pump dryers, electric induction stoves
- Resilience Strategies: Backup power, passive survivability
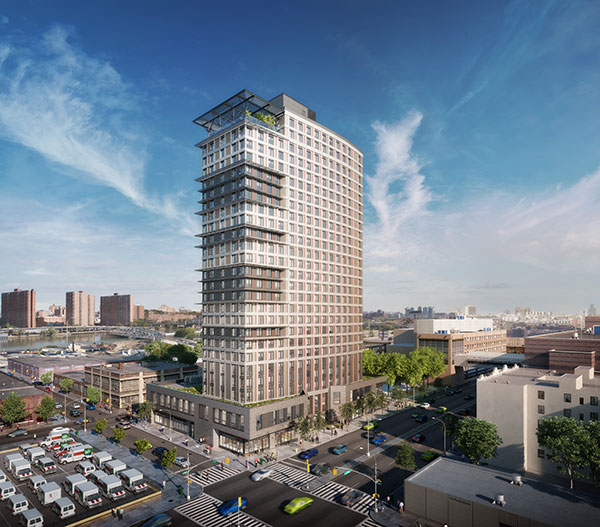
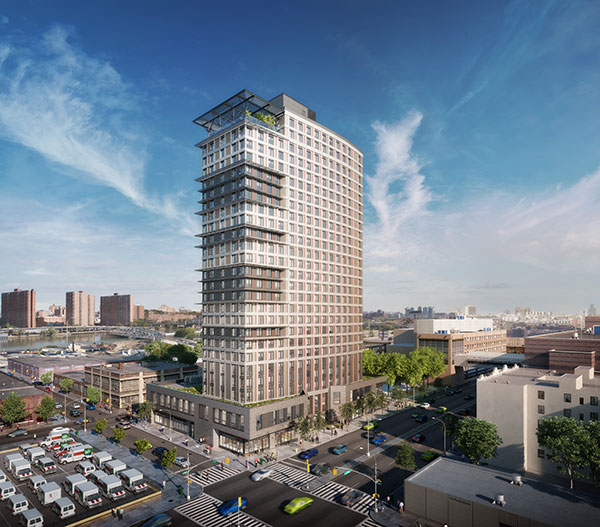
425 Grand Concourse building rendering.
Project Details
- Location: Bronx, New York
- Project Area: 310,758 sq. ft.
- Number of Buildings: 1
- Number of Stories Per Building: 26
- Number of Units: 277
- Project Cost: $121,942,998
- Cost per Gross Square Foot: $392.41
- Market Sector: Low-to-Moderate Income
- Construction Type: New Construction
- Construction Start Date: January 2020
- Completion Date: August 2022
- REDC Region: New York City
- Developer: Trinity Financial Inc.
- Architect & Design Team Lead: Dattner Architects D.C.P.
- Technologies Used: VRF, ERV, Smart Building controls
- Predicted Site Energy Use Intensity (EUI): 22.1 kBtu/SF/yr
- Net Site Energy Use Intensity (EUI): 22.1 kBtu/SF/yr
- Predicted Renewable Production Intensity (RPI): N/A
- Energy Code Baseline: 2016 NYS Energy Conservation Construction Code (ECCC)
- Performance Path: PHIUS
- Certification: Enterprise Green Communities (EGC), PHIUS+ 2015
Planning and Design Approach
Project Goals
425 Grand Concourse began from a 2015 New York City Department of Housing Preservation and Development (HPD) call for proposals to create affordable housing in a mixed-use building on a city-owned site. The project team designed this project with the intention that it would serve as an example of the commercial and operational viability of high-rise Passive House projects for affordable housing. By adhering to the PHIUS+ certification standard, this project will significantly reduce energy use and carbon emissions.
Project Team
While Dattner Architects D.C.P. is the design team lead, the developer, Trinity Financial, Inc., was significantly engaged with the project team throughout the entire design process and initiated an integrated design approach. They were included in the careful selection of the sustainability, energy, and Passive House consultant, Steven Winter Associates, Inc., and the mechanical engineer, Dagher Engineering, at the beginning of the design process. At the schematic design phase, the team conducted a Passive House feasibility study to assess what it would take to achieve Passive House certification and which Passive House certifying body to choose. This selection was made after interviewing both PHI and PHIUS+ representatives about the underlying model parameters of each organization’s compliance software to ensure that the requisite performance model would closely align with the expected program conditions (in this case, occupancy, and intensive apartment use).
Monadnock Construction was brought on to the team as the general contractor in the design development phase to ensure the project would be feasible to (1) build with widely available trades, (2) reduce the risk of construction delays, and (3) maintain the project budget. Monadnock conducted a cost-benefit analysis early on to ensure the viability of the backup wall system. The full-design team reviewed the air barrier document sets developed for both 50% and 100% construction phases. Trinity Financial found that engaging teams that are willing to make design adjustments allows for a flexible project and design process, ultimately resulting in both meeting design goals and reducing costs.
Building Design
425 Grand Concourse is a mixed-use, mixed-income affordable housing project. The massing and site are designed to integrate the project into the existing urban fabric. The tower’s north-south sculptural shape will minimize shading on the adjacent Garrison Park. The ground floor entrances and material transparency activate and engage the street front. Faceted and varying in color, the metal panel cladding provides articulation that breaks down the large scale of the building.
The building contains nonresidential spaces that will become assets for both residents and the surrounding community, including an educational facility, a health clinic, a cultural facility, retail space, and a comfort station for the adjacent and newly renovated Garrison Park. The project also encourages residents to lead an active lifestyle by including 155 indoor bike parking spaces and a fitness room.
The design team is committed to creating a sustainable and energy-efficient building. The project is on track to exceed the mandatory number of requirements for the Enterprise Green Communities (EGC) 2015 certification. The efficient energy recovery ventilation (ERV) system brings in continuous fresh air and removes stale air, while exchanging energy between the two streams to precondition the incoming fresh air. The domestic hot water (DHW) boilers’ combustion gases and dryer vents remove stale air directly outdoors to ensure improved indoor air quality (IAQ). Low-flow water fixtures, cold water leak detection attached to the building’s risers, and efficient irrigation are implemented to conserve water. To manage waste materials during construction, a waste hauler experienced with off-site sorting and materials reclamation will ensure that at least 50% of nonhazardous waste is recycled.
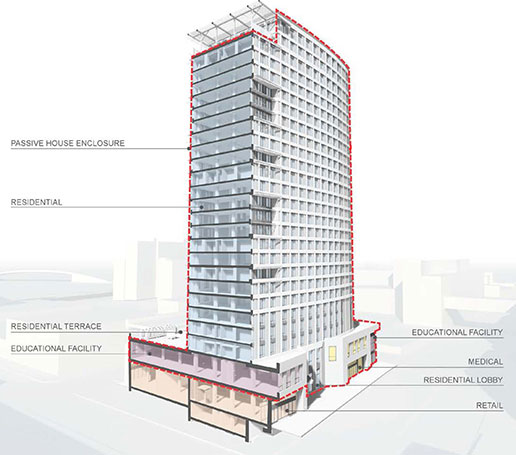
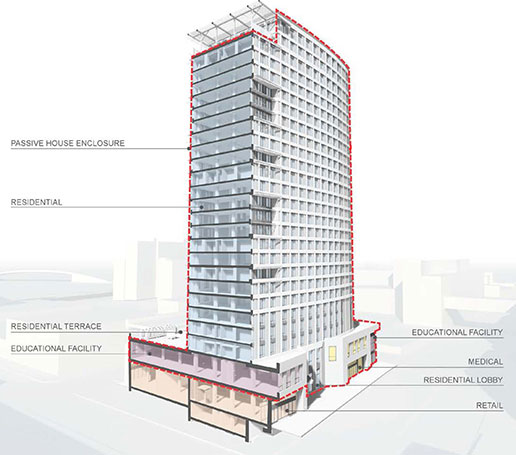
Building program diagram by Dattner Architects D.C.P
Energy Modeling
The energy model meets all the PHIUS+ 2015 certification targets. The model assumes that the building will meet the air leakage target, but this will also be verified on site after construction is complete. During construction, a few floors received windows with aluminum spacers due to a communication error, which increased the U-factor of the windows by about 0.01. Dishwashers were also added for marketability. These changes were modeled to increase source energy use by 3.5%, although the hot water savings from the dishwashers are not captured in the model. Overall, the building serves as a model for how to effectively employ Passive House strategies and efficient HVAC equipment to minimize energy use in high-rise buildings. The energy modeling inputs and results are as follows:
Energy Model Inputs | |
Certification Path | PHIUS+ 2015 |
Software | WUFI v3.2.0.1 |
CFA (% of Gross) | 246,198 SF (79%) |
HVAC | Central HVAC, Mitsubishi VRFs, 3.5 COP |
ERV | Swegon Gold, SRE of 0.83 |
DHW | 3 Gas condensing boilers |
Windows | U-factor: 0.32, SHGC: 0.27 |
Walls | R-20 |
Basement | R-20 |
Roof | R-33 |
Thermal | Bridges Included (wall and roof) |
Additional Loads | Elec. exhaust dryer, range |
Energy Model Results | Target | Modeled |
Source Energy (kBtu/SF-yr) | 63.1 | 59.7 |
Heating Demand (kBtu/SF-yr) | 3.6 | 3 |
Peak Heating Load (Btu/hr-SF) | 3.9 | 3.9 |
Cooling Demand (kBtu/SF-yr) | 5.7 | 5.7 |
Peak Cooling Load (Btu/hr-SF) | 4.5 | 3 |
Air Leakage (CFM/SF at 50 Pascals) | 0.08 | 0.08 |
Energy Efficient, All-Electric Design
High-Efficiency Lighting Fixtures and Appliances
425 Grand Concourse includes high-efficacy LED lighting throughout the building, both interior and exterior. To support the team’s goal to remove gas for end use wherever possible, each unit comes equipped with a heat pump dryer and induction cooktop.
Building Envelope
The highly efficient building envelope was designed to meet the PHIUS+ certification’s strict performance requirements. The assembly includes:
- Triple-pane windows with a U-factor of 0.32 and solar heat gain coefficient (SHGC) of 0.27—a lower SHGC is helpful in a cooling-dominated building
- 28% window-to-wall ratio
- R-18.5 above grade walls
- R-29.4 roof assembly
- Continuous thermal barriers and air barriers
- A carefully detailed envelope system to minimize thermal bridging
The envelope is designed to be extremely airtight and energy efficient, limiting noise and heat transfer. Most low-rise residential buildings in New York are heating dominated. Their relatively low internal gains and high exterior surface to volume ratio mean that the internal gains are too low to offset heat loss through the building envelope.
In contrast, due to its dense design and high-performing envelope, this mixed-use, high-rise building’s internal gains are not only sufficient to offset the small amounts of heat loss during the winter but even make the building cooling dominated most of the year. To reduce solar heat gain, large-scale sunshades were installed on the south façade. The envelope construction details are similar to standard details, with limited and targeted differences, allowing the assembly to be easily replicated with standard trades and trade practices.
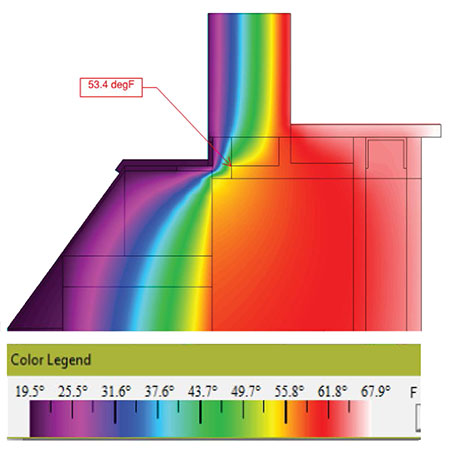
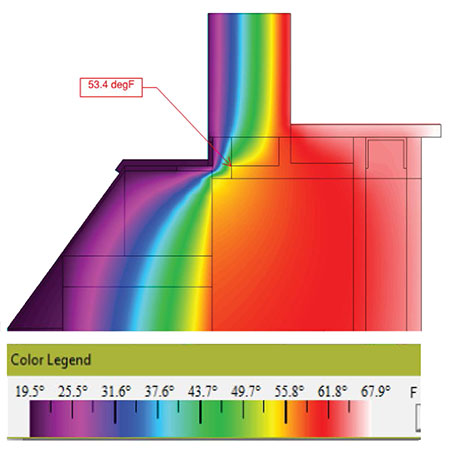
Thermal transfer diagram showing temperature change from 19.5°F to 67.9°F.
Thermal analysis of building envelope by Dattner Architects
All-Electric Systems
The all-electric heating and cooling system will be a highly efficient variable refrigerant flow (VRF) air source heat pump (ASHP) system with heat recovery. The system is ideal for this project given its high level of efficiency at such low loads.
The biggest challenge to achieving total electrification of a multifamily building of this size is the DHW system. The convention is to use centralized gas fired boiler plants with hot water recirculation to meet the building’s water heating load. Switching over to electric hot water while maintaining the building’s high performance would require centralized heat pump water heaters that are large and efficient enough to meet the building’s water heating load in the summer and, more critically, winter season when heat pump performance is reduced. Heat pump water heater (HPWH) options for this type of building were limited in the United States market when equipment selection was finalized. As a result, the project team has designed a gas-fired condensing boiler that maximizes recirculation efficiency, reducing fossil fuel consumption.
Energy Consumption Feedback and Smart Building Technologies
Trinity Financial engaged Bright Power to develop a “dashboard” for tenants that allows them to review their own detailed electrical and cooling energy consumption data. It will be presented as an anonymous comparison to average units of that type in the building. The development team plans to give half of their tenants access to these “dashboards” to see whether having access to personal consumption data influences energy consumption behavior.
New residents will be given an orientation to explain the energy-saving components that come equipped within the units. They will also receive a “Resident’s Green Building Guide” before moving into their apartments, which will explain the sustainable and high-performing features incorporated throughout the building. In parallel, a building maintenance manual will be developed for the management team to provide instructions for the proper maintenance of the equipment, ensuring all building systems are performing optimally.
The common areas and back of house spaces have bi-level lighting with occupancy sensors. The exterior lights have photocell control, and all corridors have daylight sensors coupled with daylighting design strategies. Cold water riser leak detection monitors are included to conserve water by quickly locating problem areas. In addition, an extensive monitoring system was installed to track indoor temperature, thermostat settings and readings, and relative humidity in all apartments and common spaces as well as energy consumption readings of all individual building equipment, such as pumps and fans, compressors, and evaporators.
In Passive House design, the only exit path for moisture is through the ventilation air streams. ERVs recover up to 70–80% of the moisture in the air stream, so there is a potential for high relative humidity levels in the wintertime during peak moisture generation times—morning and evening rush hours. To avoid high wintertime humidity levels, the ERVs utilize a custom designed control scheme. When relative humidity levels in the exiting exhaust air stream exceed a threshold that would allow condensation at the façade’s interior surface (e.g., the windowsill), the exhaust air will temporarily bypass the energy recovery core to prevent the transfer of relative humidity to the incoming air stream. It is expected that this situation will only occur during a handful of exceptionally cold winter nights per year. The expected energy-recovery loss of these events (and therefore loss of some energy efficiency) through the bypass scenario is minimal. ERVs also come equipped with a free-cooling “summer bypass” mode, which activates when the exterior air temperatures are favorable.
Commissioning
Intermediate field testing of critical building envelope components—such as windows and roof connections—will be performed. The building’s mechanical systems will be commissioned to ensure (1) proper ventilation flow rates are achieved at all constant airflow regulator (CAR) dampers and ERV units, (2) that the VRF system’s control schemes are set up and running properly, and (3) that the water systems are balanced and running efficiently. Quality control during construction will be enforced by the general contractor through inspection, and intermediary air tightness tests of critical façade geometries will be conducted by Steven Winter Associates.
Building Operations
Leasing Structure
425 Grand Concourse is located within an extremely low-income census tract, making affordable housing crucial to the area. The project is committed to providing the majority of units to the low- to moderate-income (LMI) population. Seventy-five percent of the apartments will be for individuals or families within 30% and 80% Area Median Income (AMI), 28 of which will be reserved for the formerly housing challenged. The remaining 25% of units will be open to those with 100% AMI. Tenants are billed for their apartment’s electricity use (which includes cooling), but heating, DHW, and water (which are not individually metered) are included in rent.
Cost Reduction
The relative cost of construction for 425 Grand Concourse is projected to be 3% more than comparable buildings, while the rental prices are 31% lower. The scope and location of this project greatly influenced the total cost. The site is under 30,000 square feet (SF), so the proposed density of 277 units and commercial space was only possible through a high-rise development, which is significantly more expensive than low- or mid-rise. The site is also located on a topographical ridge and next to a subway tunnel. These conditions require rock excavation, transit authority-related engineering, vibration monitoring, and railroad insurance, further increasing the construction cost.
There is currently limited data on Passive House high-rise construction cost, performance, and economic viability, so this project aims to show that Passive House is a replicable solution by providing much of the needed data, details, construction methods, and lessons learned to the high-density housing development and construction community.
Additional Benefits
Site Context
425 Grand Concourse is located in the South Bronx and has many nearby resources for residents, including the Lincoln Hospital Greenmarket, Health Opportunities High School, Garrison Playground, and the Universal Hip Hop Museum. There are also many restaurants, shops, and pharmacies in the near vicinity. Four bus stops are located within 0.2 miles of the site, and five subway stops within 0.5 miles. The adjacent Walton Avenue also has a bike lane. The area has a Walk Score of 93/100 and a Transit Score of 100/100. With a density of over 135 units per acre, the project’s density is much higher than the surrounding neighborhood, which generally has about 17 units per acre.
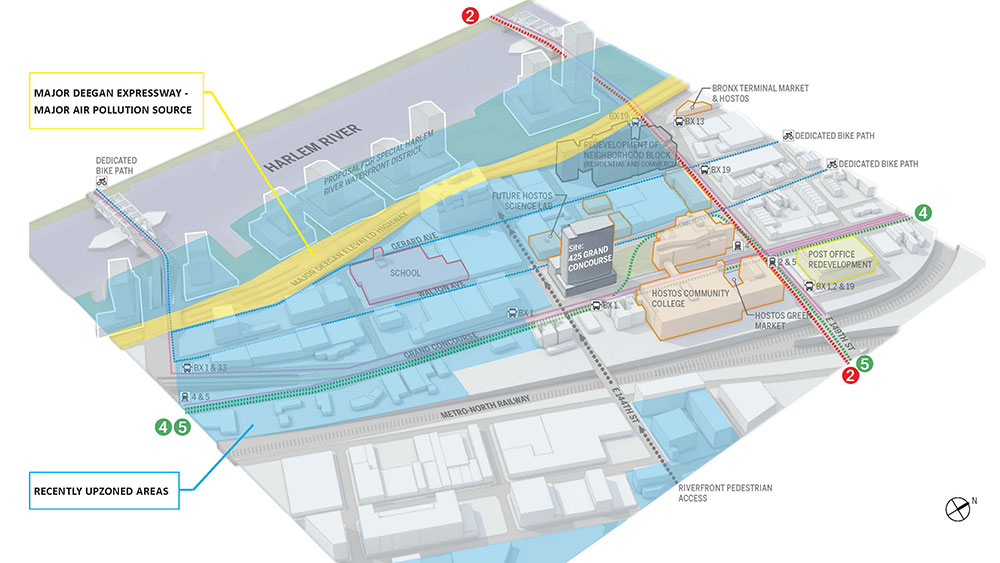
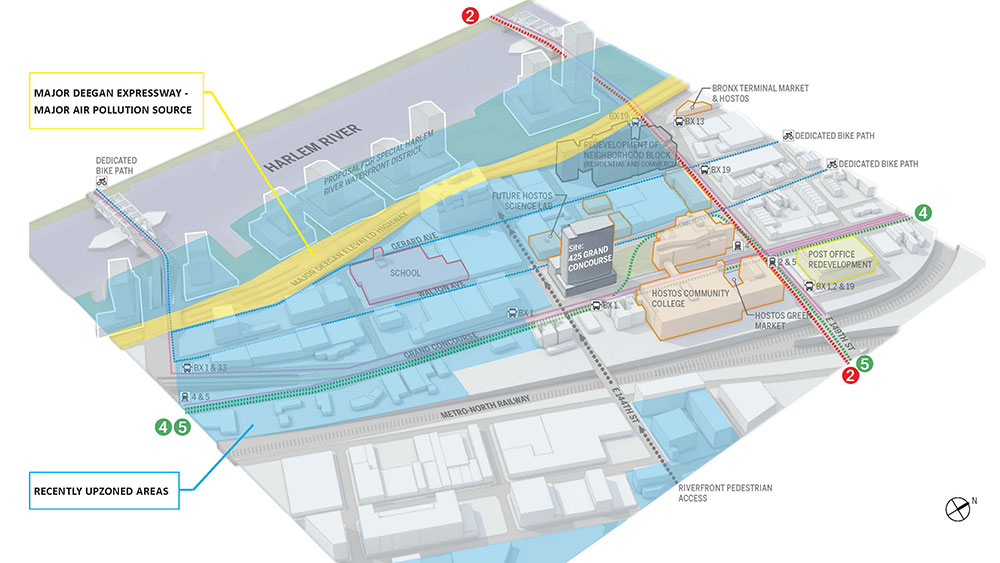
Site and context diagram by Dattner Architects
Occupant Health, Comfort, and Productivity
The area around the site contains sources that emit significant air pollution like solid waste transfer stations and highly trafficked roadways. The high-quality ERV system will allow residents to have fresh, filtered air continuously supplied to the building’s interior spaces. DHW combustion equipment and dryer exhaust will be vented directly outside. Using electric induction cooktops, rather than gas, eliminates a major and very common source of indoor air contamination. The resulting enhanced IAQ will have fewer indoor pollutants and allergens, which can decrease the risk of asthma, a disease that disproportionately affects disadvantaged communities. The building itself will have fewer emissions using the VRF system. The airtight and continuously insulated building envelope will reduce outdoor-to-indoor noise transmission, eliminate drafts and cold interior surfaces, and limit temperature fluctuations, keeping the interior environment quieter, more comfortable, and safer.
Resiliency
Designed to PHIUS+ certification standards, 425 Grand Concourse is expected to be extremely durable and have a prolonged lifespan. The high-performance design, particularly the high-quality and airtight envelope components, ensure the building will remain resilient in the case of extreme weather or an extended period without power. For instance, in a winter power outage, the envelope system will retain heat inside the building, keeping interior temperatures at safe levels—above 50°F—for several days, minimum. These attributes increase the building’s passive survivability, meaning that the building will remain safe and livable without active systems or power for a longer period of time. The temperature retention qualities of the high-performing enclosure also limit the risk of freeze damage to the building components. For example, during the 2021 Winter Storm Uri in Texas [PDF] , many residents experienced significant flooding damage due to burst frozen pipes and about one-third of all Texans experienced water damage in some form. Altogether, the storm caused between $80 billion and $130 billion in financial losses to the state economy.
Experience from Superstorm Sandy of 2012 has shown that high-rise buildings are especially vulnerable to prolonged power outages as emergency power systems typically only address short-term emergency loads, but not longer-term loads required for sheltering in place. For example, the water pressure in the street can supply water to approximately the fourth floor without supplemental pumping. Without domestic water kitchens and bathrooms, and therefore entire apartments were made uninhabitable on higher floors. This project includes a gas-fired emergency generator sized to provide code-required emergency power (e.g., fire alarm, emergency lighting, and evacuation elevator use) as well as longer-term power for limited elevator use (important for accessibility, seniors, and families with young children), domestic water pumps, access control, limited electrical plug loads on every residential floor, and WiFi use near the building lobby to allow for basic communications. In the case of a summer power outage, active night-time window air flushing will keep the interior temperatures from getting too high, keeping the building safe for occupancy. Additionally, all of the corridors on residential floors have daylighting, limiting the reliance on artificial lighting, which increases interior visibility during grid outages.
Lessons Learned
As the largest PHIUS+ project among certified and pre-certified projects to date, this project has many unique design details and lessons learned:
- Integrated design: At the onset of the project, Trinity Financial engaged the entire design team and specifically selected both the sustainability/energy/Passive House consultant (Steven Winter Associates) and the mechanical engineer (Dagher Engineering) with the goal of ensuring the project’s success as a Passive House certified building. Having Monadnock Construction at the table during the project’s design proved to be an integral part in ensuring the project would be feasible to build with widely available trades, while avoiding delays and cost overruns.
- Centralized domestic hot water (DHW): The biggest challenge of complete electrification of high-rise multifamily buildings is the DHW system because heat pump water heater options at that scale are very limited in the U.S. market.
- DHW recirculation: The centralized hot water recirculation layout was carefully designed to help reduce the water heating load. Given the project’s size, and in particular its height, the system is split into two main zones. The team selected a “box design” where a horizontal loop is located at the upper floor in addition to the typical loop on the lower floor. As compared to the more conventional and less efficient “3-pipe design” this system has half as many vertical hot water recirculation risers. The box design, along with strategically clustered water taps, drastically reduced the recirculation piping and subsequent losses within the building. This translates to significant hard and soft cost savings for expensive copper piping as well as water heating and cooling costs through reduced heat loss from the hot water recirculation system within the Passive House envelope.
- Centralized energy recovery ventilation (ERV): A centralized ERV system will result in significant cost savings (both upfront and operational), while still allowing the team to achieve its Passive House certification goal. Maintenance concerns were a key motivation in the selection of centralized ERVs. Intake louvers must be cleaned regularly and due to the building’s height, these would not be accessible in a decentralized system.
- Variable refrigerant flow (VRF) design: The team is utilizing wall mounted indoor evaporator units, and where feasible, a floor mounted unit located at a partition wall between a bedroom and the living room to match the VRF indoor unit capacities to the building’s especially low loads. This will limit short cycling, which can hinder the system’s longevity, and enhance summertime dehumidification capacity. Branch controllers also supply entire floors, allowing for concurrent cooling in some spaces (e.g., eastern exposure in the morning) and heating in others (e.g., western spaces in the morning). The requisite loads can be offset on the floor level of the branch controller, and ideally will not trigger the use of the roof-mounted condenser unit.
- Concrete masonry unit (CMU) backup wall: Prefabricated mega panels were considered early in the design process because the controlled assembly environment ensures a high-quality production and the panels would have provided Trinity with a single-source warranty on the entire building envelope. However, relying on a single fabricator, the panels would need to be installed in sequence and any error or damage to a panel would halt the installation process until it could be refabricated and delivered. This posed too much of a risk to the tight construction schedule and would have substantially limited competitive bidding. In addition, a tower crane would have been needed for installation which in turn would have increased construction cost significantly. Instead, the development team collaboratively designed a wall section that enabled on-site assembly by standard building trades. The non-load-bearing CMU backup wall allows for weatherproofing the facade entirely from the interior. This is advantageous in high-rise construction since the interior can be built out in a dry and tempered environment while the superstructure is still in construction. In contrast, the superstructure must be completed before the erection of scaffolding to enclose other types of exterior wall
- Considering renewables: The project team evaluated the potential for on-site photovoltaics (PV) early in the project’s design. Given the limited roof availability and high-density nature of the project, PV would offset a very small percentage of the building’s energy load, so it did not make economic sense.
Ready to get started on new construction?
Contact NYSERDA at [email protected].